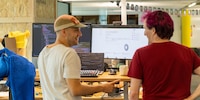
Behind the scenes
More AI, more price transparency – dispatches from Hackfest
by Martin Jungfer
Our packaging machines make mistakes too. But last year there were so many wrong deliveries that we had to intervene. Our newest packaging machine, Packo Rabanne, was sent to detention.
It was our After Sales Service who first noticed that something was wrong. The autumn before last, the team informed us that they were registering an above-average number of returns – but only for orders processed by the packaging machines. Now, you’d think robots don’t make mistakes. But they do. This could be, for example, because a product gets mixed up somewhere in the machine.
Up to this point, however, there had been only a few incorrect deliveries. Suddenly, we were confronted with a massive increase. Compared to the many packages we send out, this is a small fraction. Even so, mistakes like this cost us a lot of money.
Shortly before we noticed the flood of errors, we started up the fourth packaging machine. After Packy McPackface, Sir Packsalot and Packie Chan, Packo Rabanne joined the team in October 2021. The obvious conclusion was that our youngster Packo was out of line and responsible for the faulty parcels. After a thorough investigation, we found that Packo was indeed the culprit.
But we were in quite the pickle; first, we had to find out where the error was actually occurring. We examined a random sample of 110 deliveries to trace back the fault. Next, we analysed the relevant customer service tickets reporting incorrect delivery. We noticed that it was always an entire series that was faulty. We set up cameras at the packaging machines to track where the error was happening. And this is how we finally uncovered Packo’s MO: after losing a product post-scanning, Packo didn’t send out an error message. Now, said lost product still goes through the entire machine, confusing the internal tracking system. As a result, Packo would print each address label offset by one parcel. This led to a chain reaction: all subsequent packages ended up with the wrong recipients. And this continued until Packo either ran out of work or the team removed a product from the packing line.
Thanks to our video analysis, we also noticed that the error often happened when two products passed through the scanner at the same time. There should, in fact, be a distance of 15 cm between products. We were able to quickly eliminate this source of error by monitoring this distance.
In addition, we trained our packing employees. Orders consisting of multiple products that go through the packaging machines are particularly prone to errors. They’ve got to be sturdily bundled so they don’t end up rolling around on the conveyor belt. We shared our findings with the manufacturer of the packaging machine, who fixed several bugs in the software. and used our feedback to revamp Packo, resulting in fewer incorrect deliveries.
Detention paid off for Packo. He’s making much fewer mistakes now. Our goal was to have him generate no more than 400 incorrect parcels per million parcels shipped. That would be an error rate of 0.04%. In November 2022, we reached this figure – right in time for the Christmas rush. And in the months since, Packo’s got even better. Bravo!
I am affectionately called the "machine whisperer" in the company, because together with my team I make sure that all our packaging machines work and do not cause any problems.