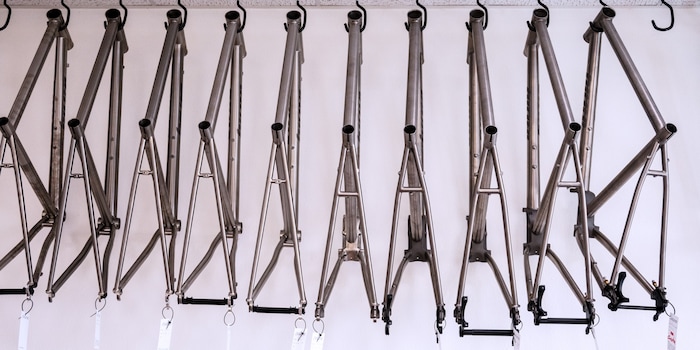
These titanium bike frames by Hilite Bikes are top-notch

A small factory in Basel produces bicycles that are 100% tailored to customers’ wishes. Hilite Bikes is one of the few manufacturers in Europe to produce its own bike frames – by hand and out of titanium.
My eyes are gleaming, my hands are a bit clammy and I’m super excited. I feel like a kid in a candy shop as I enter the Hilite Bikes store in Basel’s Gundeli District. Company founder and CEO Biagio Colletto has been selling his bikes here since 2010.
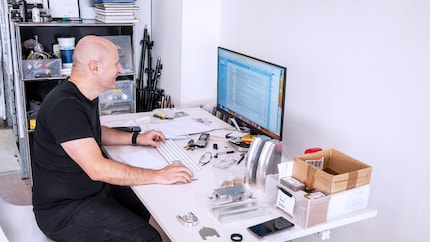
Source: Patrick Bardelli
Craftsmanship at its finest
It all started 14 years ago with standard frames made of carbon and aluminium, which were manufactured for Hilite Bikes in Taiwan. In 2012, the manufactory designed the first titanium frame for a customer and had it built in a specialised workshop. Today, Biagio Colletto and his team produce between 30 and 40 bikes a year in Basel. About half of them come with made-to-measure titanium frames. In addition to custom frames, Hilite Bikes also develops standardised bike frames and complete bikes that can be adapted to customers’ wishes. Most of them are made of titanium, some of aluminium and carbon.
Be it racing bikes, gravel bikes, tandems, mountain bikes or special touring bikes, they’re all available here. In the back of the shop, which serves as a small bike workshop, the bicycle mechanic is currently busy assembling a touring bike. In a few days, a customer from Finland will pick it up personally and ride it back to the far north. The custom bike business is international and, according to Biagio, works mainly through word of mouth. With a small team of just a few employees, Hilite Bikes generates an annual turnover in the mid-six-figure range.
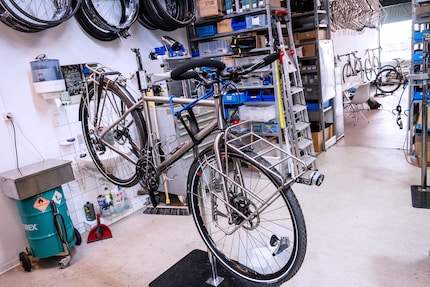
Source: Patrick Bardelli
Why titanium?
In addition to the usual derailleur gears by Shimano, Sram and the like, the Basel-based company also offers hub gears by Rohloff and bottom bracket gears by Pinion and combines them with belt drives by Gates. «Why titanium?» I ask Biagio Colletto. «In my opinion, it’s the perfect material for building bicycles,» the chemical engineering graduate answers. «On the one hand, because it’s quite light compared to other types of metal, while offering similar flex. As a result, a titanium bike offers a comfortable ride quality. On the other hand, because titanium is more sustainable than carbon.» Biagio Colletto goes on to say that a titanium frame is practically indestructible, doesn’t rust and boasts a beautiful shiny finish. Nothing wrong with looking good!
Hilite Bikes only uses carbon for the fork, especially for racing bikes and gravel bikes. Carbon is less flexible than titanium, offering more stability when cycling at high speeds.
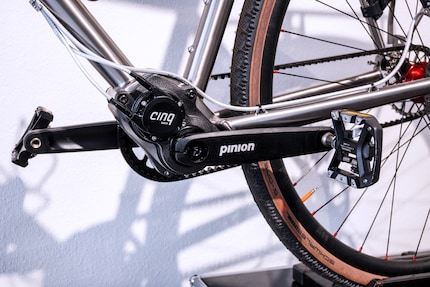
Source: Patrick Bardelli
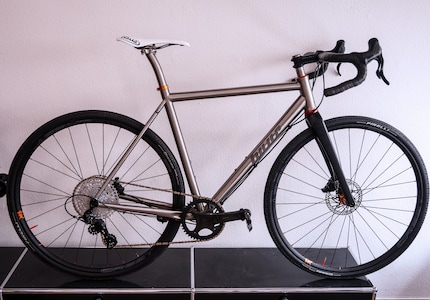
Source: Patrick Bardelli
Behind the scenes of the workshop
The actual Hilite Bikes is workshop located on the Dreispitz site, not far from the shop. Biagio and I set off to visit it – on two Hilite bikes, of course. This turns the mundaneness of a short change of location into an enjoyable activity.
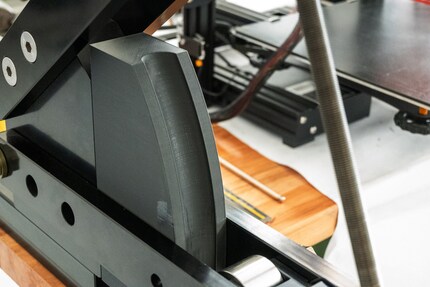
Source: Patrick Bardelli
Once in the workshop, Biagio Colletto explains how the titanium blanks are turned into a finished bicycle frame. This involves bending, milling, turning and, of course, welding and is done by a fine metal mechanic and a specialised welder. In very simplified terms, this is the process: with gas tungsten arc welding (GTAW) the tube is filled with argon gas. Gas is heavier than air, thus forcing the air out of the pipe. The individual parts are then welded together. Theoretically, it’s possible to weld without gas. However, this would produce weld joints of poorer quality than those produced with the gas method.
Biagio currently has a request from a customer who’s 2.04 metres tall and is looking for a bike with Rohloff hub gears. An XXL standard frame by Hilite would be an option. However, customers often have other wishes, such as additional attachment points for bikepacking bags. That’s how the need for a custom-made frame arises.
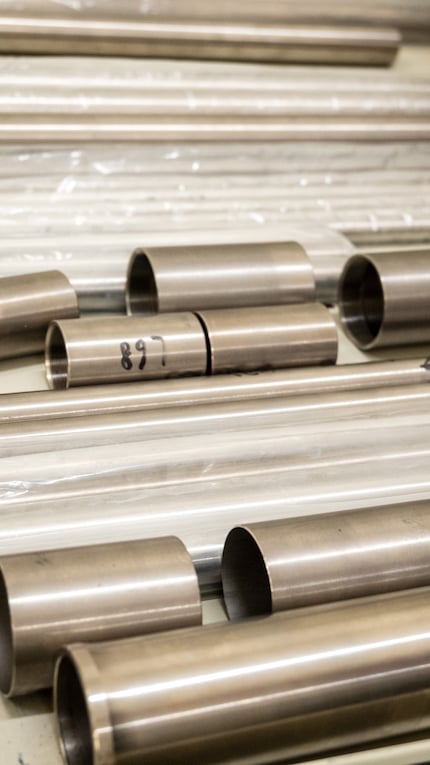
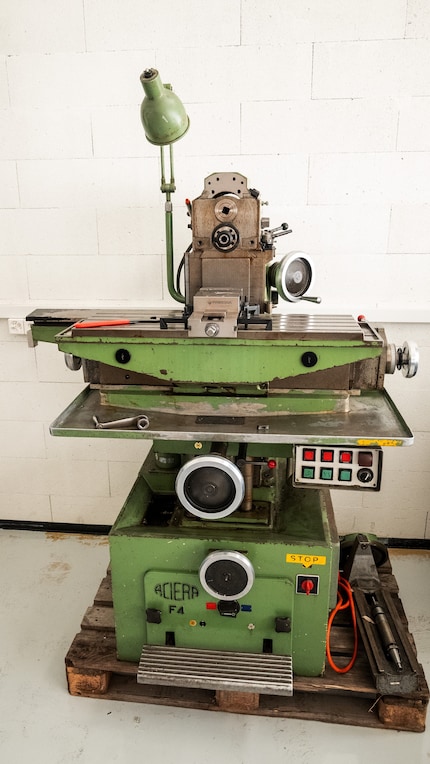
Source: Patrick Bardelli
Biagio usually sends his customers to the Basel Crossklinik for a professional bike fitting. There, the 3D motion capture system by Retül is used to measure the cyclist’s body angles. Based on this data, Hilite Bikes designs the perfect bike for this person and welds the frame accordingly.
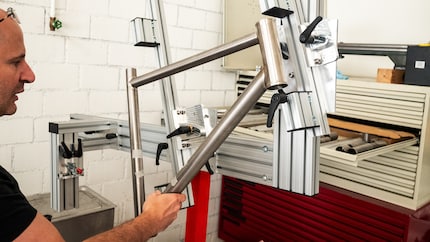
Source: Patrick Bardelli
The geometry of the bike is one thing; the look and the riding behaviour are another. It all comes down to how a customer will use their bike and, of course, how much they’re willing to spend. These aspects also define the choice of components, such as the type of wheels, or whether the bike is equipped with a chain drive or a belt drive.
Biagio’s bikes are in great demand. There’s a long waiting list, which is processed chronologically. For a standard frame, the waiting time is a few weeks; for a custom-made frame, it’s between three and five months, depending on the type of bike and design. A Hilite bike costs between 8,000 and 14,000 francs. What about special requests? For example, if a customer wants the fork to be the same colour as their car? Biagio Colletto and his team will make it possible.
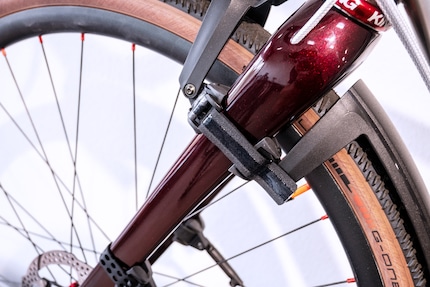
Source: Patrick Bardelli


From radio journalist to product tester and storyteller, jogger to gravel bike novice and fitness enthusiast with barbells and dumbbells. I'm excited to see where the journey'll take me next.